一、正佳精机冲子机设计规划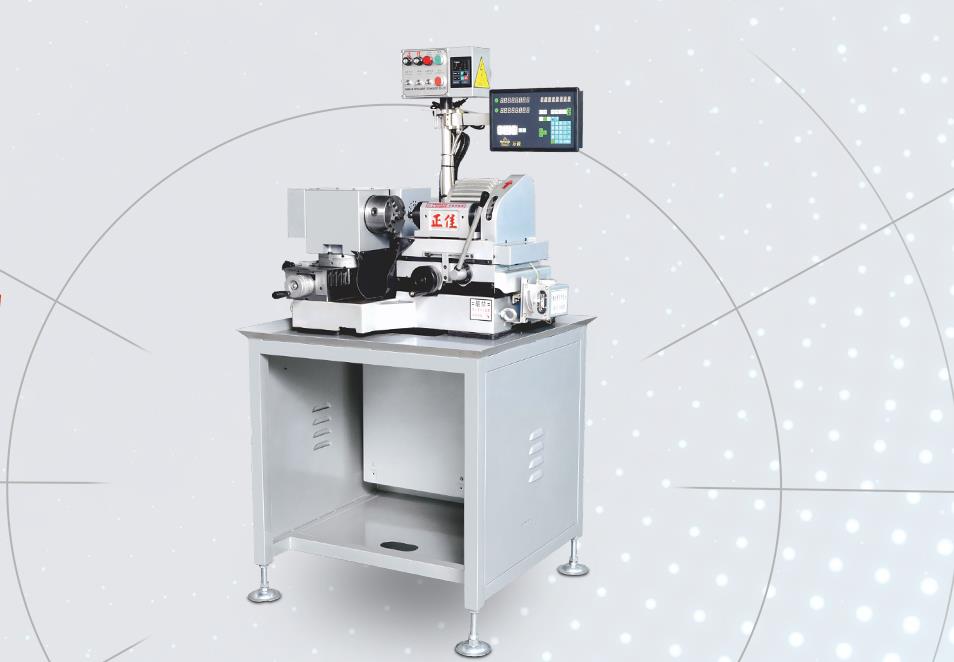
需求分析
根据市场需求、客户要求和行业标准,确定冲子机的性能指标、规格参数和功能特点。例如,明确冲子机的冲压力、冲压速度、加工精度、适用材料等。
考虑冲子机的使用环境和操作便捷性,以便设计出符合实际生产需求的产品。
方案设计
由专业的工程师团队进行冲子机的整体方案设计。这包括机械结构设计、电气控制系统设计、液压或气动系统设计等。
绘制详细的设计图纸,包括装配图、零件图等,确保各个部件的尺寸、形状和配合精度准确无误。
二、原材料采购
确定材料清单
根据设计要求,列出冲子机生产所需的各种原材料清单,包括钢材、铝材、电气元件、液压元件、传动部件等。
明确各种材料的规格、型号、数量和质量要求。
供应商选择
寻找可靠的原材料供应商,对供应商的资质、信誉、产品质量和价格进行评估和比较。
与选定的供应商签订采购合同,确保原材料按时、按质、按量供应。
三、零部件加工
机械加工:使用各种机床设备,如车床、铣床、钻床、磨床等,对钢材等原材料进行切削、加工,制造出冲子机的各个机械部件,如机身、滑块、冲头、模具等。
严格控制加工精度,确保各个部件的尺寸公差、表面粗糙度等符合设计要求。
电气元件组装
对采购的电气元件进行检测和筛选,确保其质量可靠。
按照电气原理图进行布线和组装,将各种电气元件安装到冲子机的控制柜中。
液压或气动系统装配
对液压元件或气动元件进行清洗和检测,确保其无泄漏、无损坏。
根据液压或气动系统原理图进行管路连接和装配,确保系统运行稳定、可靠。
四、整机装配
部件检验
对加工好的各个机械部件、电气元件和液压或气动系统进行检验,确保其质量符合要求。
对不合格的部件进行返工或更换,确保整机装配的质量。
整机装配
将各个机械部件按照装配图进行组装,安装好传动系统、润滑系统、冷却系统等。
将电气控制系统和液压或气动系统与机械部分进行连接和调试,确保各个系统协同工作。
五、调试与检测
空载调试
对冲子机进行空载运行调试,检查各个部件的运动是否顺畅、电气控制系统是否正常、液压或气动系统是否稳定。
对调试过程中发现的问题进行及时调整和修复。
负载调试
进行负载运行调试,使用实际的材料进行冲压加工,检验冲子机的冲压力、冲压速度、加工精度等性能指标是否符合设计要求。
根据负载调试结果,对冲子机进行进一步的调整和优化,确保其性能稳定可靠。
质量检测
对冲子机的各项质量指标进行全面检测,包括外观质量、尺寸精度、机械性能、电气性能等。冲子机是一种用于制造冲子(如冲压模具中的冲头)的设备,其生产流程大致如下:
冲子机设计阶段:
对冲子机的各个部件进行详细设计,包括机身结构设计,要确保足够的刚性和稳定性以承受加工过程中的冲击力;设计冲子的夹持装置,使其能够牢固地夹紧不同规格的冲子毛坯;设计刀具系统,选择合适的刀具类型(如砂轮、铣刀等)及其安装方式,以实现冲子的有效加工。例如在设计冲子夹持装置时,要考虑能够快速换装不同直径的冲子,并且在加工过程中保证冲子不会发生松动或偏移。
零部件制造阶段
原材料采购:
根据设计要求,采购合适的原材料。机身部分可能选用高强度的铸铁或钢材,以保证结构强度;传动部件如齿轮、丝杆等可能选用优质合金钢,以满足耐磨和精度要求;电气控制系统的元器件则需采购符合相关标准且质量可靠的产品。
比如采购符合 GB/T 9439 标准的灰铸铁来制作冲子机机身,确保其具有良好的铸造性能和机械性能。
机械加工:
对采购的原材料进行机械加工,通过切割、车削、铣削、磨削等工艺将原材料加工成设计所需的各个零部件形状。例如,将钢材加工成具有精确尺寸和形状的机身框架、传动部件等。
在加工过程中,要严格按照设计图纸和工艺要求进行操作,控制加工精度,使用量具(如卡尺、千分尺等)进行实时测量,确保每个零部件的尺寸偏差都在允许范围内。
热处理:
部分零部件如刀具、重要的传动部件等,需要进行热处理以提高其硬度、强度和耐磨性等性能。热处理工艺包括淬火、回火、调质等。
例如对铣刀进行淬火处理,使其硬度提高,能够更有效地切削冲子毛坯材料,然后再进行回火处理,以消除淬火产生的内应力,提高刀具的韧性。